Aluminum window extrusion profiles are essential components for window construction, offering durability, customization, and energy efficiency for modern architecture.
Key takeaways:
- Aluminum window extrusion profiles offer durability, customization, and energy efficiency.
- Selecting the right aluminum alloy and temper is crucial.
- Thicker profiles provide better insulation and strength.
- Recyclability reduces environmental impact.
- Design factors include thermal performance, structural integrity, aesthetics, and more.
- Aluminum provides strength, resistance to corrosion, energy efficiency, and easy maintenance.
- Quality control steps ensure durability and functionality during manufacturing.
Material Selection for Aluminum Window Extrusion Profiles
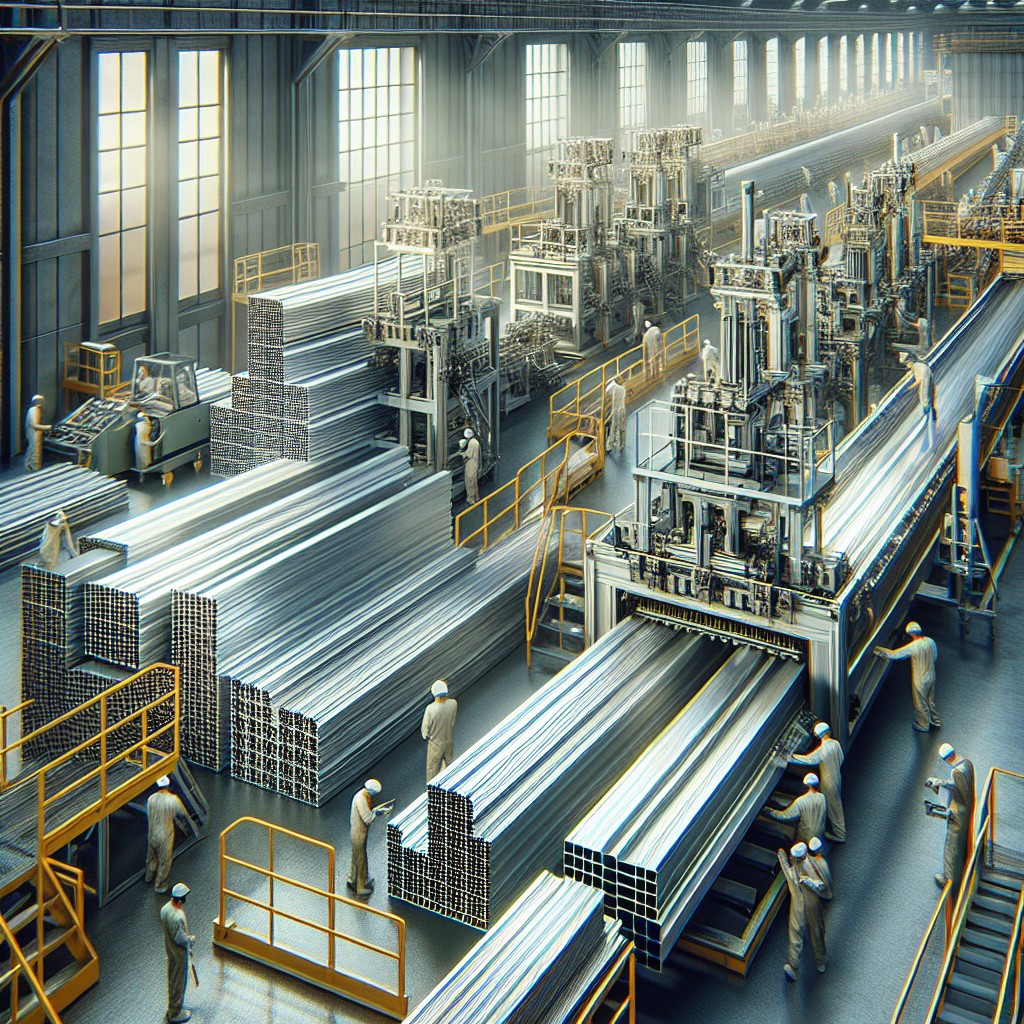
Selecting the right aluminum alloy for window extrusions is a critical step. The industry typically uses the 6000 series alloys, which offer the right balance between strength, corrosion resistance, and workability. Among those, the 6063 and 6061 are prevalent due to their good mechanical properties and surface finish after anodizing, enhancing the product’s aesthetic appeal and durability.
The aluminum’s temper also plays a role in the performance of the window profile. Tempers such as T5 and T6 indicate how the aluminum was treated to achieve certain mechanical properties. T5 means that the aluminum has been cooled from an elevated temperature shaping process and then artificially aged. T6, on the other hand, means that the aluminum was solution heat-treated and then artificially aged. This treatment results in a material that is more durable and less likely to warp.
Moreover, the aluminum’s thickness impacts both insulation and structural integrity. Thicker profiles provide better insulation and strength but can increase material costs and require more substantial hardware to support their weight.
Recyclability adds to aluminum’s appeal, reducing the environmental impact of aluminum window frames. Most aluminum alloys used in window extrusions contain a high percentage of recycled material without compromising performance.
Selecting superior quality aluminum ensures longer lifespan, lower maintenance, and improved energy efficiency in window systems. It’s a balance between cost, performance, and sustainability that determines the ideal material choice for each extrusion project.
Designing Aluminum Window Extrusion Profiles
When creating aluminum extrusion profiles for windows, designers must consider several vital factors:
- Thermal Performance: Extrusions can feature thermal breaks – insulating material between the inner and outer aluminum sections – to improve energy efficiency.
- Structural Integrity: Profiles should withstand environmental pressures, including wind and thermal expansion, without compromising their form or function.
- Acoustic Insulation: Design considerations may also include the reduction of sound transmission for a quieter interior.
- Aesthetics: Options range from slim, minimalistic lines to more substantial, classic designs to complement various architectural styles.
- Drainage: Incorporating weep holes and sloped shapes ensures water egress, preventing the accumulation that can lead to damage.
- Compatibility with Hardware: Profiles must accommodate locks, handles, hinges, and opening mechanisms, which determines the ease of use and security of the window.
Effective design of aluminum window extrusion profiles demands a balance of these elements to deliver exceptional performance and user satisfaction.
Benefits of Aluminum for Window and Door Profiles
Aluminum stands out for its strength-to-weight ratio, providing robust window frames without the bulk. This feature enables larger glass panes within sleek profiles, optimizing natural light and outdoor views. Additionally, the material’s innate resistance to corrosion safeguards windows from harsh weather conditions, ensuring long-term structural integrity and appearance.
From an energy efficiency perspective, thermal breaks in aluminum profiles reduce heat transfer, contributing to stable indoor temperatures and potentially lower energy bills. It’s worth noting that aluminum is highly recyclable, offering a sustainable option for eco-conscious consumers.
Maintenance demands are minimal, as the non-porous surface repels dust and dirt, requiring just a simple wipe-down for cleaning. Furthermore, the flexibility of aluminum allows for an array of finishes, including powder coating and anodizing, which can match any architectural style while enhancing durability.
Lastly, fire resistance is a critical yet often overlooked advantage, with aluminum able to withstand high temperatures without releasing harmful substances.
Quality Control in Manufacturing Aluminum Window Profiles
Maintaining high standards during the manufacturing of aluminum window profiles ensures durability and functionality. Quality control involves several key steps:
1. Material Inspection: The aluminum billets used must meet industry standards for composition and purity. Any variance can affect the extrusion process.
2. Dimensional Accuracy: During extrusion, dimensions are continuously monitored. Even minor deviations can compromise the structural integrity and performance.
3. Surface Finish: A thorough evaluation for visual defects such as scratches or dents is crucial. Coating thickness is measured to guarantee proper corrosion resistance.
4. Mechanical Testing: Samples are subjected to stress tests, verifying the strength and resilience of the profiles under various load conditions.
5. Thermal Performance: For energy-efficient windows, the profiles undergo testing to ensure they provide adequate insulation.
It’s a rigorous process designed to meet stringent industry benchmarks, safeguarding the reputation of manufacturers and the satisfaction of end-users.
Recap