In the realm of manufacturing, structural foam molding stands as a method of choice for creating lightweight, durable products with a high strength-to-weight ratio. This technology is an industry secret weapon, making it possible to fabricate intricate parts that can’t be produced with other molding techniques.
Despite its intricacy, structural foam molding remains a complex yet critical process, often misunderstood by those outside the manufacturing sphere. We’ll explore the applications across various sectors, compare it with traditional methods, and look ahead to future innovations.
Process Steps
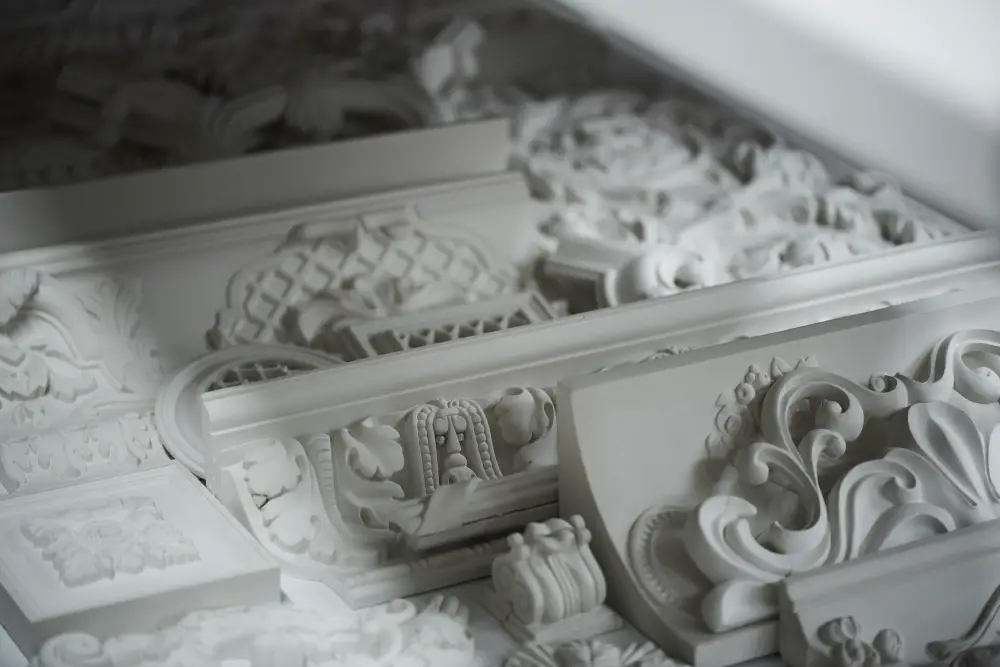
Pre-expansion
The process begins with the thermoplastic pellets loaded into a hopper and then heated to a specific temperature. Once melted, the material is pressurized and injected with a small amount of blowing agent. This creates a suspension of tiny cells in the resin, expanding it before it’s injected into the mold. The pre-expanded material has improved flow properties, enabling faster, more efficient molding.
Injection
The pre-expanded material is then injected into the mold cavity at a lower concentration. This allows the material to fill the mold with less force than required for traditional injection molding.
Cooling and Solidification
After the mold is filled, it is cooled with water or air, causing the foam to solidify. The resulting part has a solid outer shell and a cellular core, which provides strength while reducing weight.
Materials Used
The foam molding process works with a wide variety of materials, including polyethylene (PE), polypropylene (PP), and certain engineering resins such as polycarbonate (PC) or polyamide (PA). These materials are chosen based on the product’s specific end-use requirements, offering manufacturers both a lightweight solution and a cost-effective alternative.
Applications in Various Industries
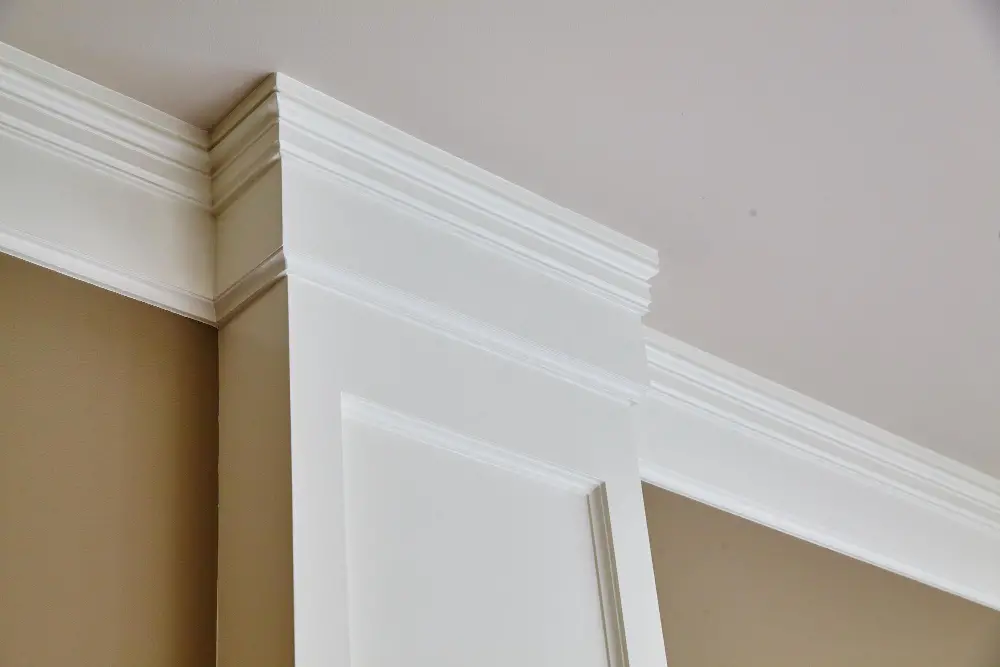
Structural foam molding has found its applications in various industries, bridging the gap between cost-effectiveness and high performance. In the automotive sector, this technology is used to manufacture components such as door panels, dashboard substrates, and bumper cores, where lightweight and durability are paramount.
The construction industry benefits from its ability to produce large, strong, yet lightweight panels and structural components that contribute to energy efficiency and easy installation. In the realm of consumer products, everything from lightweight yet sturdy furniture to protective packaging materials and toys are produced using this versatile process.
Furthermore, the technology’s adaptability and efficiency have paved the way for its use in creating critical medical devices and equipment, highlighting the process’s importance across a broad spectrum of applications.
Lightweight yet Strong Products
Perhaps the most notable advantage of structural foam molding is its ability to produce parts that are significantly lighter while retaining a high level of structural integrity. This is particularly beneficial for applications that require the transport or handling of large components.
Namely, structural foam molding is created lighter, so it consumes less material, reducing costs and making it an environmentally friendly choice. When compared to traditional molding techniques, structural foam molding allows manufacturers to use thinner walls while still achieving the same level of strength.
Cost-effectiveness
The efficiency of the foam molding process, which allows for quicker cycle times and lower material costs, translates to overall production savings. The technique also minimizes the need for secondary processes due to the incorporation of features during molding.
A lot of the work is done in the mold, which eliminates the need for additional machining or assembly processes. Additionally, due to its ability to produce large components with thin walls and high strength, structural foam molding can reduce material usage by up to 50% compared to traditional methods.
Design Flexibility
Foam molding enables a high level of design freedom, allowing manufacturers to create parts with variable wall thicknesses and complex design features. This means engineers and designers can innovate with design complexity without concern for increased weight or production complications.
In case of any design changes, the mold can be easily altered as needed to accommodate them, making structural foam molding an ideal choice for prototyping and product development.
Advantages over Traditional Injection Molding
One of the primary advantages structural foam molding offers over traditional injection molding is the reduction in stress and warpage of the manufactured parts. The pressure used in foam molding is considerably lower, which significantly reduces internal stresses that often lead to warpage or dimensional instability in products made with traditional molding methods.
This characteristic is particularly beneficial for producing large, complex parts where maintaining dimensional accuracy is critical. Furthermore, structural foam molded parts exhibit superior thermal insulation properties due to the foam’s cellular core structure.
This can be a crucial factor in applications requiring temperature control or insulation. The reduced density of the parts also contributes to better acoustic insulation, a desirable trait in multiple industries such as automotive and construction.
Nevertheless, it’s clear that structural foam molding is more than just a manufacturing process; it’s a robust solution that addresses several critical industry needs – from reducing material costs and improving product performance to enhancing design flexibility and environmental sustainability.
Its applications across automotive, construction, consumer products, and medical sectors showcase its versatility and the significant value it adds to products in terms of strength, lightweight features, and cost savings. Looking towards the future, as industries continue to seek efficient, sustainable, and innovative manufacturing methods, structural foam molding is poised to play a pivotal role.
With ongoing advancements in materials science and process technology, its potential applications are set to expand even further, marking it as a key technology in the evolution of modern manufacturing.
Related Stories
- The Journey of Recycled Window Glass
- uPVC vs WPC Doors: Which Is Better?
- A Guide to Selecting the Right Metal for Your Home Project
- Quality Construction Products Are Essential for Project Success
- When to Replace Your Roof: Signs That It’s Time for a New One
Recap